The primary difference between enameled copper wire and enameled aluminum wire is their electrical conductivity and mechanical properties.
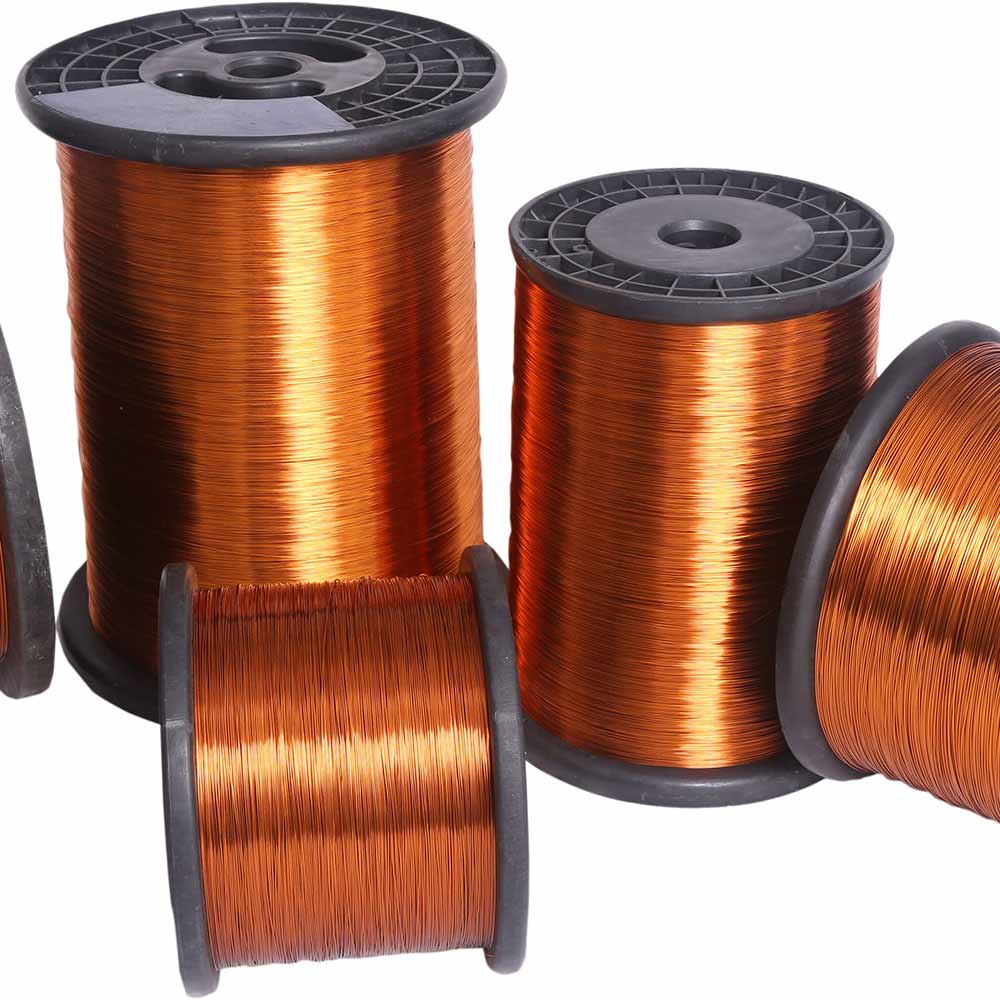
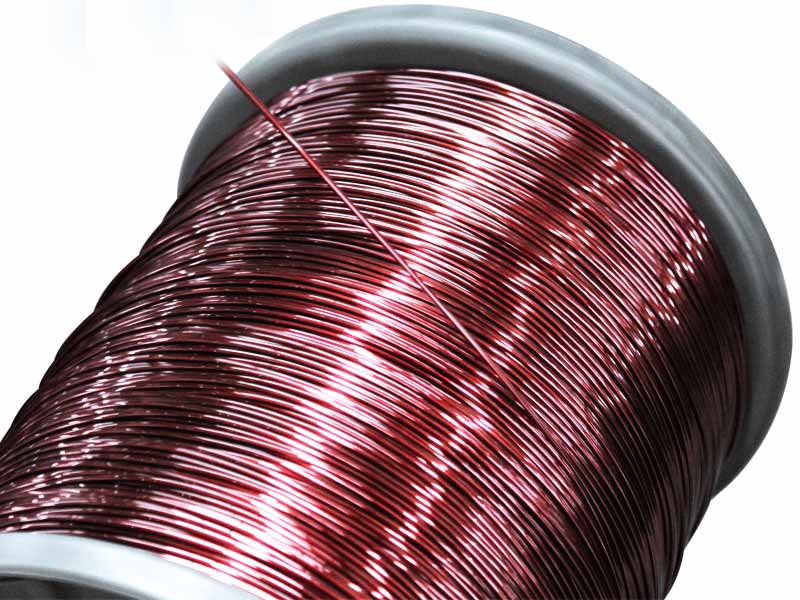
Enameled copper wire has higher electrical conductivity than enameled aluminum wire, which makes it a better conductor of electricity. Copper wire is also stronger and more durable than aluminum wire, which makes it better suited for applications where the wire is subject to mechanical stress, such as winding coils for motors and transformers.
Enameled aluminum wire is less dense than enameled copper wire, which makes it lighter and more cost-effective. It also has a higher thermal conductivity, which makes it better suited for applications where heat dissipation is important, such as in transformers and other electrical devices. Additionally, aluminum wire is less prone to oxidation and corrosion than copper wire, which can make it a better choice for applications where the wire is exposed to harsh environmental conditions.
In terms of application, enameled copper wire is commonly used in high-performance motors, transformers, and other electrical devices where high conductivity and mechanical strength are required. Enameled aluminum wire is often used in applications where weight and cost savings are important, such as in the production of coils for speakers and other audio equipment.
Overall, both enameled copper wire and enameled aluminum wire have their own unique properties and applications, and the choice between the two will depend on the specific requirements of the application.