Improved Performance And Reliability In Conductors With Plated Coatings
Conductive materials are the backbone of modern electronic devices, and their reliable and stable performance is essential for seamless communication and data transfer. Copper or copper-based alloys are commonly used as conductors due to their excellent electrical conductivity and mechanical properties. However, certain applications require additional properties to be added to the wire, such as corrosion resistance or solderability. To meet these requirements, plating techniques are commonly used to apply a coating onto conductive materials. This article discusses the different types of plated coatings and their applications.
Typical plated coating types:
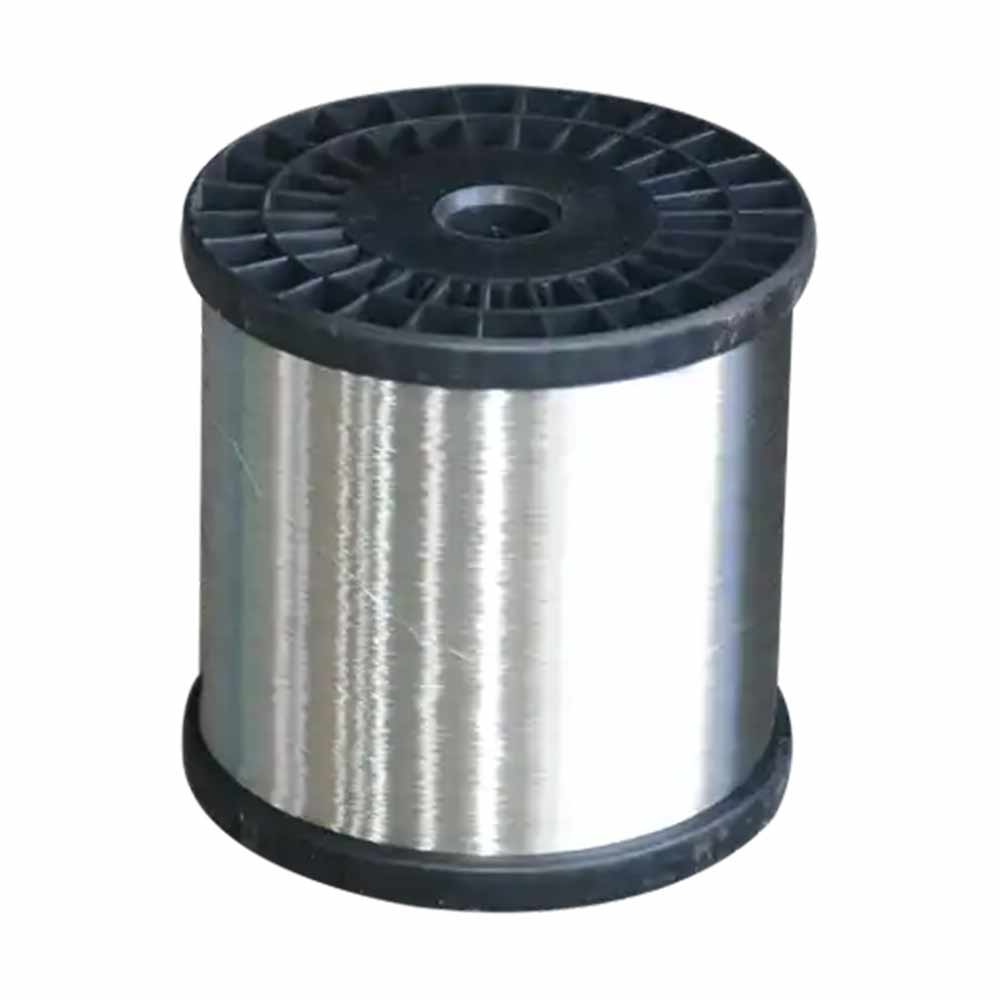
Tin Plating
Tin is the most common coating used over copper wires due to its low cost and excellent solderability. Tin also improves the wire’s chemical resistance and reduces the rate of corrosion (depending on the thickness of the coating). However, tin has a lower melting point than copper, so it provides little improvement to the temperature range of the conductor. A disadvantage of tin coating is that it forms an inter-metallic layer when plated over copper, which increases resistance compared to bare or silver-plated wire.
Copper Plating
Copper plating is often used to improve the conductivity of less conductive metals or to add a conductive layer onto non-metal substrates like plastics. It also provides excellent solderability and improves the wire’s surface hardness, wear resistance, and ductility. Copper plating has a similar melting point to copper and is therefore capable of extending the temperature range of the conductor. However, copper oxidizes readily and requires a barrier layer to avoid the oxidation and reduce the formation of intermetallic compounds.
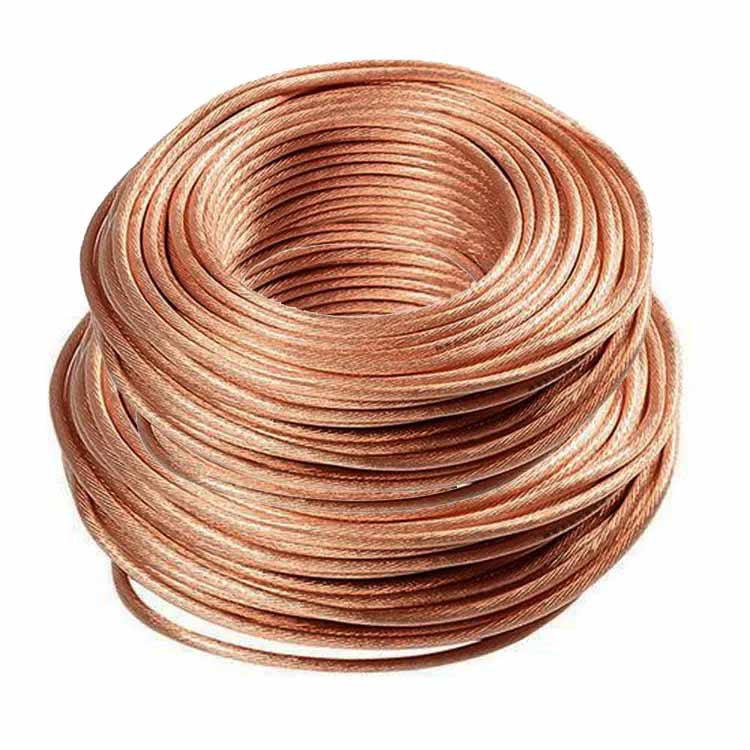
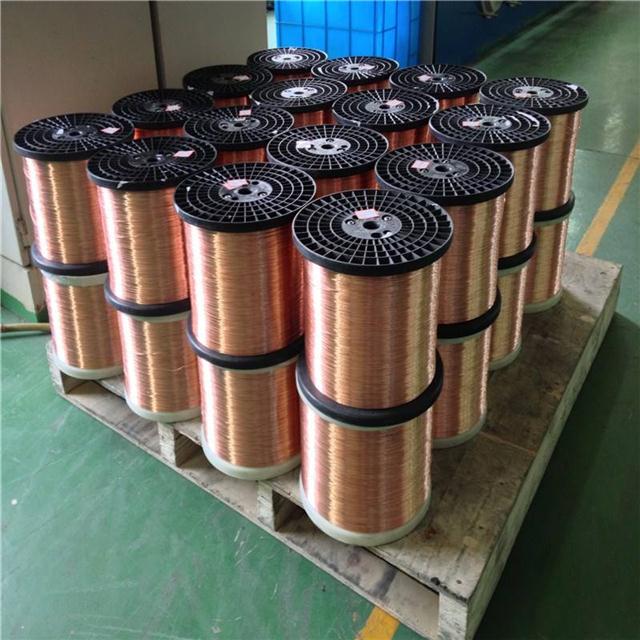
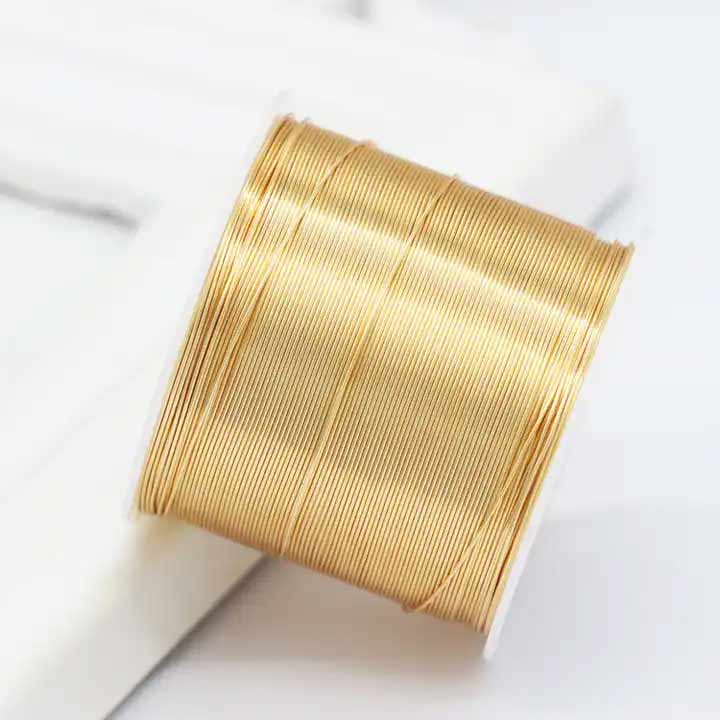
Gold Plating
Gold plating is used for applications requiring high reliability and longevity, such as aerospace, medical devices, and high-end audiovisual equipment. Gold provides excellent corrosion resistance, high electrical conductivity, and low contact resistance, making it an ideal choice in environments with harsh temperature and abrasive conditions. The disadvantages of gold plating include its high cost and the fact that it is a relatively soft metal, which may cause problems during handling and installation.
Silver Plating
Silver is one of the best conducting metals and offers extremely high conductivity to plated wire, reducing the wire’s resistance. This property can be particularly beneficial in high-frequency applications where increased current flow through the silver due to the skin effect can enhance performance. Other advantages of silver plating include increased high-temperature performance and improved chemical resistance. The solderability of silver-plated conductors is excellent, and the impact of oxidation on solderability is minimal as silver oxide is a conducting material. However, silver plating is more expensive than other plating options.
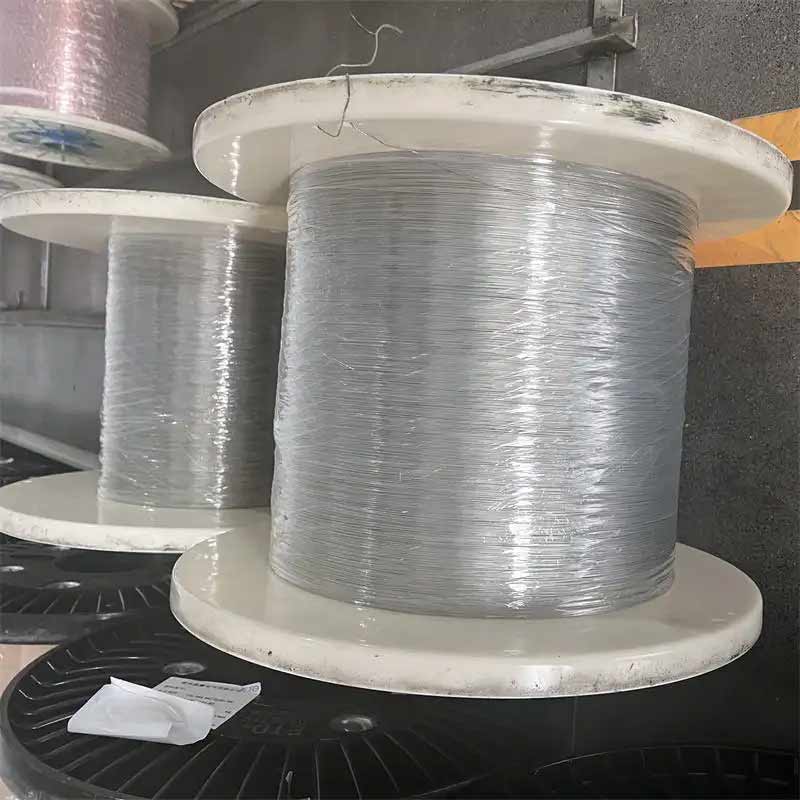

Nickel Plating
Nickel is a much harder metal than the other common plating options and offers excellent resistance to high temperatures. The increased temperature range due to nickel plating depends on the thickness of the plating but is superior to that gained by using silver. Nickel is very resistant to harsh environments and corrosion, but soldering it can be difficult and requires an activated flux. The conductivity of nickel is relatively low, and plating will increase the resistance of the wire, much like the impact of tin plating.
Application Considerations:
When choosing the type of coating for conductive materials, several factors must be considered. These include:
Conductivity
The primary function of coated conductors is to transfer electric current. Therefore, the coating material should have excellent electrical conductivity to minimize the loss of current during transmission.
Solderability
In many applications, a conductive material is joined with another part through the process of soldering. The ability of the coating to accept solder will determine how well the components attach to each other.
Chemical Resistance and Corrosion
Conductive materials must withstand exposure to chemicals and moisture that may damage metals. The coating material must be able to protect the conductor from the harmful effects of these agents.
Temperature Resistance
Some applications require the conductor to operate in high-temperature environments. The coating material should be able to withstand high temperatures without losing its integrity.
Conclusion
Plated coatings provide better performance and reliability for conductive materials in various applications. Different types of coating materials offer unique advantages and disadvantages, and selecting the right one requires careful consideration of the properties and application requirements. By understanding the different types of coatings and their benefits, manufacturers can produce high-quality conductive materials with improved performance and reliability.
You may also interested in
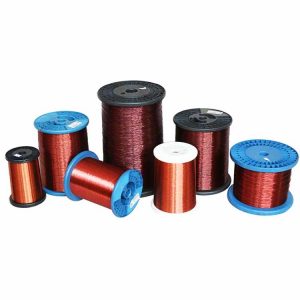
difference between enameled copper wire and enameled aluminum wire
The primary difference between enameled copper wire and enameled aluminum wire is their electrical conductivity and mechanical properties. enameled copper wire Enameled copper wire has higher electrical conductivity than enameled aluminum wire, which makes
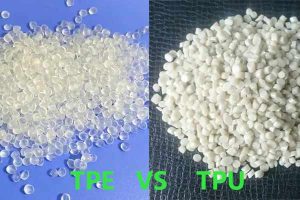
how to distinguish TPE and TPU -4 easy methods
How to Distinguish TPE and TPU-4 Easy methods The performance of TPE and TPU are quite similar and cannot be distinguished by the naked eye, but they can be distinguished by some simple methods. Looking
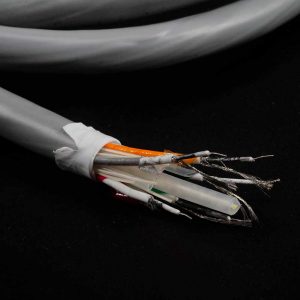
how to choose cable for injection overmoulding TPE cable VS TPU cable
How to choose Cable for overmold-TPE cable VS TPU Cable Cable used in Medical devices interconnection or medical accessories can be silicone cable, TPE cable or TPU cable. Of course PVC cable can also be