parylene c coating-the ultimate parylene coat for Medical silicone Cable Biocompatible
Parylene C Coating is a proces for a Parylene Coat which is a perfect solution for Medical Silicone Cable ,which solve the Silicone Dust Sticky and Biocompatibility at the same time.
In the medical industry, the demand for high-performance, reliable, and biocompatible materials is paramount. Parylene C coating has emerged as the ultimate solution for medical silicone cables, addressing critical issues such as silicone dust stickiness and biocompatibility simultaneously. As a professional medical wire harness manufacturer, we recognize the unparalleled benefits of Parylene C coating in enhancing the performance and safety of medical devices. This article delves into the properties, processes, and applications of Parylene C coating, highlighting why it is the go-to choice for medical silicone cable applications.
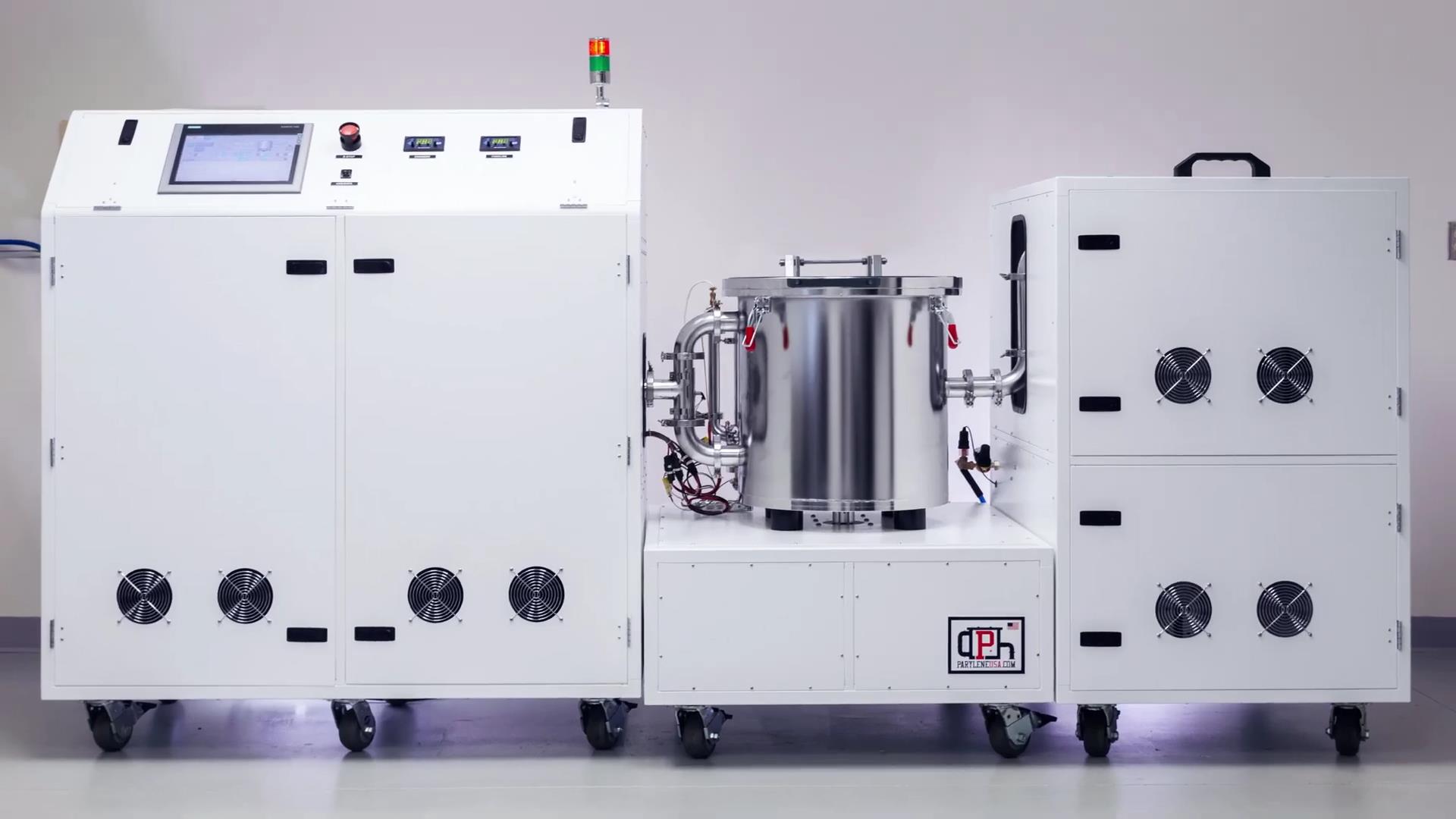
Parylene C coating device
Why Parylene C Coating is the Ultimate Solution for Medical Silicone Cables?
Parylene C coating is a specialized Parylene coat that provides a perfect balance of protection and biocompatibility. It effectively solves two major challenges in medical silicone cable manufacturing:
- Silicone Dust Stickiness: Silicone surfaces often attract dust and particles, which can compromise the performance and cleanliness of medical devices. Parylene C coating creates a smooth, non-stick surface that prevents dust accumulation.
- Biocompatibility: Medical devices must meet stringent biocompatibility standards (e.g., ISO 10993). Parylene C coating is FDA-approved and biocompatible, making it ideal for applications involving direct or indirect contact with the human body.
While Parylene N coating is also used in medical applications, Parylene C stands out due to its superior moisture resistance and chemical inertness, making it the ultimate choice for medical silicone cables.
A Comprehensive comparison of Parelene type
Key Properties of Parylene C Coating
Parylene C coating offers a unique combination of properties that make it indispensable in the medical industry:
- Moisture Resistance: With a water vapor transmission rate of just 0.08 g/m²/day, Parylene C provides exceptional protection against humidity and liquid exposure.
- Chemical Inertness: It resists corrosion from disinfectants, bodily fluids, and other chemicals commonly encountered in medical environments.
- Biocompatibility: Compliant with ISO 10993 standards, Parylene C is safe for use in implantable devices and other medical applications.
- Mechanical Protection: The coating is highly flexible and durable, protecting cables from abrasion, bending, and other mechanical stresses.
The Parylene C Coating Process
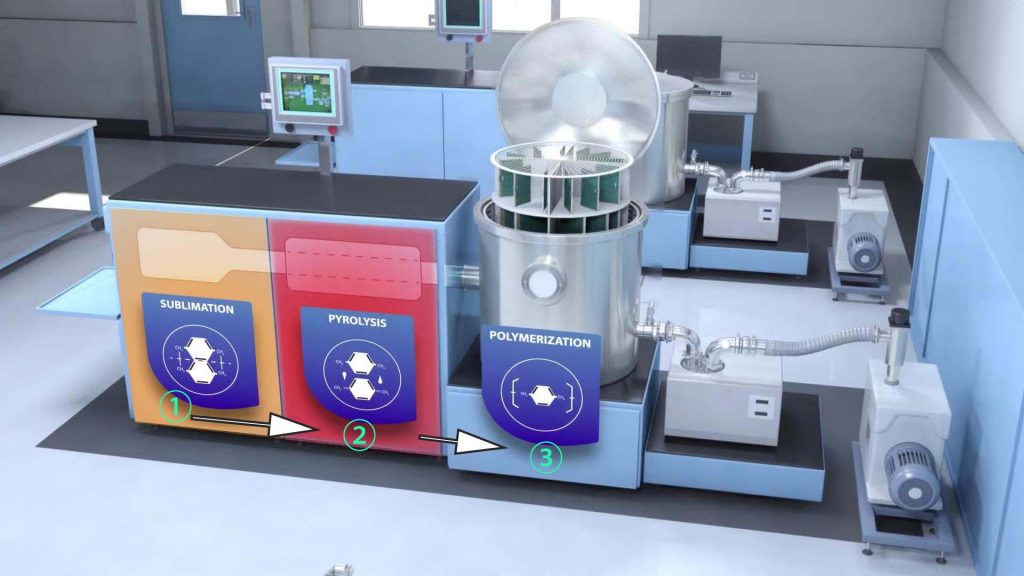
The Parylene C coating process involves a chemical vapor deposition (CVD) technique, which ensures uniform and pinhole-free coverage. Here’s a step-by-step overview:
Vaporization: Solid Parylene C dimer is heated to form a vapor.
Pyrolysis: The vapor is broken down into monomeric form at high temperatures.
Deposition: The monomeric gas is deposited onto the substrate (e.g., medical silicone cable) at room temperature, forming a thin, uniform Parylene coat.
Curing: The coating adheres firmly to the substrate, creating a durable protective layer.
Applications of Parylene C Coating in Medical Wire Harnesses
Parylene C coating is widely used in various medical applications, particularly for medical silicone cables. Here are some examples:
Endoscope Cables: The coating ensures smooth operation and prevents contamination during procedures.
Gastroscope Wires: Parylene C protects against chemical exposure and enhances biocompatibility.
Surgical Tool Wires: It provides mechanical protection and resistance to sterilization chemicals.
Implantable Devices: The coating ensures long-term reliability and safety in devices like pacemaker leads.
Benefits of Parylene C Coating in Medical Applications
Enhanced Durability: Extends the lifespan of medical cables.
Improved Performance: Ensures reliable signal transmission and electrical insulation.
Reduced Maintenance: Minimizes the need for frequent cleaning and replacement.
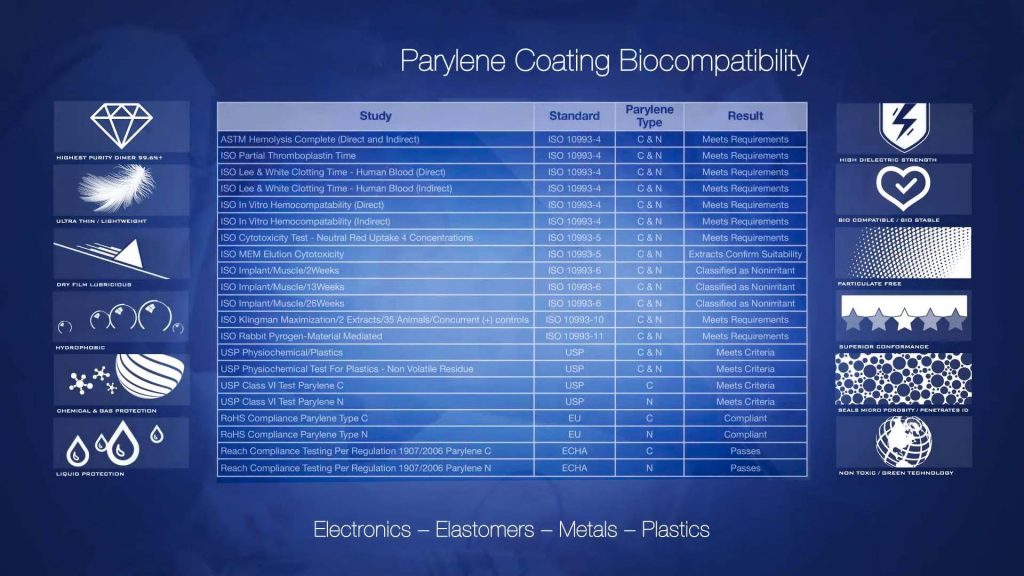
Parylene C coating is the ultimate solution for medical silicone cables, offering unmatched protection, biocompatibility, and performance. Its ability to address silicone dust stickiness and meet stringent biocompatibility standards makes it indispensable in the medical industry. As a leading medical wire harness manufacturer, we rely on Parylene C coating to deliver high-quality, reliable products that meet the demands of modern healthcare.
FQA
The most often used Parylene coatings are Parylene C and Parylene N; each have unique properties for specific use. Detailed comparison will enable you to understand their variations:
①, chemical makeup:
• Parylene N: Parylene is a pure hydrocarbon structure in essentially basic form. Its traits are low dielectric constant and dielectric properties.
• Parylene C: Derived from Parylene N chemically with a chlorine atom. This change increases moisture and chemical resistability.
②. Made weatherproof
• Parylene N: Provides less efficacy than Parylene C. yet great moisture resistance.
• Parylene C: Because of its better moisture barrier properties, ideal for high-humidity conditions including medical equipment exposed to body fluids.
③. Chemical-proof
• Parylene N is perfect for low chemical exposure levels since she has little chemical resistance.
• Parylene C: Perfect for severe medical disorders since she is rather resistant to solvents, acids, and bases.
④- dielectric characteristics
• Parylene N: With her low dielectric constant and great strength, ideal for high-frequency electrical uses.
• Parylene C has rather less dielectric properties than Parylene N.
⑤: biocompatibility
Though less well-known than Parylene C., Parylene N is biocompatible and fit for medical use.
• Parylene C: perfect for direct body contact medical equipment since FDA-approved and biocompatible.
Parylene N. finds use in high-frequency electronic components like sensors and communication systems.
Because of its great moisture and chemical resistance, parylene C is often utilized in surgical tools, silicone cables, and implanted devices.
Although Parylene C and Parylene N offer exceptional protection and performance, Parylene C is advised for medical uses only because of her moisture and chemical resistance and biocompatibility. But high-frequency electronic devices needing dielectric properties gain from parylene N.
Parylene C coating improves medical silicone cable performance, durability, and safety. Medical silicone wires have issues this complex coating solves:
①In humid conditions,such ase operating rooms and sterilization, medical silicone cables can fail electrically and absorb moisture.
The Parylene C coating effectively prevents moisture with a water vapor transfer rate of 0.08 g/m²/day. This ensures constant performance in damp conditions.
②Medical silicone cables can disintegrate when exposed to powerful chemicals including sterilizers, bodily fluids, and disinfectants.
Parylene C coating prevents corrosion and extends cable life.
③For patient safety, medical equipment must meet ISO 10993 biocompatibility standards.
Medical silicone cables for implanted devices or direct-contact applications can be coated with FDA-approved biocompatible Parylene C.
④.Medical silicone cables bend, strain, and abrade during installation and use.The cable’s flexible and robust Parylene C. covering prevents mechanical wear.
⑤. Reduced Silicone Dust Stickiness: Dust and particles on silicone surfaces can affect medical device cleaning and operation.
Parylene C coating keeps wires clean and effective by preventing dust buildup.
⑥.Medical silicone cables need good insulation to carry signals and prevent short connections.The enhanced dielectric strength and electrical insulation of Parylene C coating ensure medical device reliability.
⑦. Applications Endoscope Cables: Parylene C coating for cleanliness and smoothness.The coating protects surgical tool wires from chemicals and prolongs life.
⑧.Implantable devices must ensure pacemaker lead safety and reliability.Parylene C coating improves medical silicone cables’ mechanical protection, biocompatibility, moisture and chemical resistance, and electrical insulation. Due to these benefits, Parylene C. coating is essential for high-performance medical usage
Healthcare professionals choose Parylene C coating for implanted devices.
The reasons are:
1. Biological compatibility
Parylene C coating is FDA-approved and ISO 10993-compliant, making it safe for long-term tissue and fluid contact. It helps pacemaker leads, neurostimulators, and cochlear implants.
2. Barrier
This layer protects implanted devices from moisture, chemicals, and bodily fluids, increasing their lifespan. The low water vapor transmission rate (0.08 g/m²/day) offers protection in humid human surroundings.
3. Flexibility, durability
Flexible Parylene C does not delaminate or shatter when bent or stretched. Body-moving devices need this.
4. Even, thin coating
A thin, homogeneous Parylene C coating is formed by chemical vapor deposition (CVD) to preserve complicated geometries without adding bulk.
5. Electrical Insulation
Dielectric properties provide the coating dependable electrical insulation for cardiac leads that demand correct signal transfer.
Parylene C coating is useful for implanted medical devices due to its biocompatibility, durability, and protection under difficult medical circumstances.